Our Mi-V partner, Digital Core Technologies (DCT), has developed a thermal Imaging Pipeline on PolarFire® SoC FPGA. The thermal Image Signal Processor (ISP) is an extremely low power and yet, powerful alternative for the thermal imaging available in other architectures. This can be tuned for various applications like Security/Surveillance, Medical imaging, Industrial Monitoring, Gas detections and others. The Pipeline is built to run on DCT’s SoM, CMSV_A1_PF254_AX. This SoM carries the PolarFire® SoC FPGA, MPFS250T, a 64bit multicore RISC-V CPU subsystem processor with FPGA fabric, DRAM, EMMC Flash, and Wi-Fi systems on board and runs on Linux Operating System.
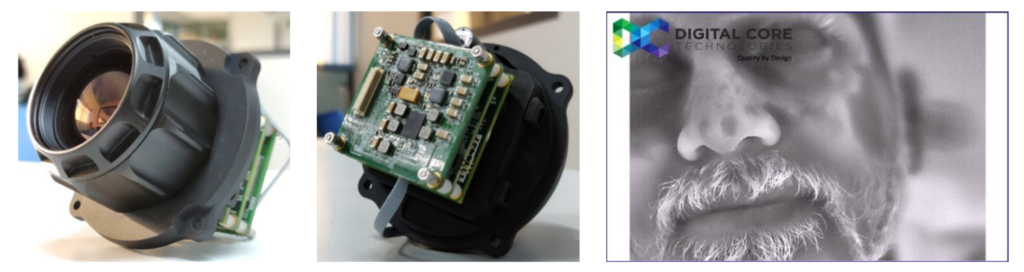
Thermography cameras usually detect radiation in the longwave-infrared (LW-IR) range of the electromagnetic spectrum (roughly 9–14 µm) and produce visual images of the thermal radiation. Since IR radiation is emitted by all objects with a temperature above absolute zero, these cameras make it possible to see one’s environment with or without visible illumination. Thermal imaging camera makes warm objects stand out well against cooler backgrounds; all warm-blooded animals become easily visible against the environment, day, or night.
Thermal cameras are widely used in defense and civilian applications. In defense sector it is mainly used for night vision applications such as gun-site and as surveillance cameras. Civilian applications include industrial inspection applications, driving assistance and medical diagnostics. Firefighters use thermography to see through smoke. Maintenance technicians use thermography to locate overheating joints and sections of power lines, and machines. Building construction technicians can see thermal signatures that indicate heat leaks in faulty thermal insulation and can use the results to improve the efficiency of heating and air-conditioning.
The most important part of a thermography camera is an IR Sensor. Focal Plane Array sensors with “uncooled microbolometers” is the most popular technology used now for the thermal imaging. The Sensor with its front-end electronics circuit is called camera core, which literally forms the core of a thermal camera.
In a thermography camera the important parts are a thermal (IR) sensor and electronic core with Imaging ISP. The core capture and condition the pixel data from the sensor and convert it into a digital stream representing an image frame. An image processing pipeline transform the stream of frames suitable for human vision.
Image processing is normally a very computation intensive task because digital images include large amount of information. Most of the architectures currently available uses high power for doing these computationally intensive digital image processing. The RISC-V based PolarFire® SoC FPGA utilizes extremely low power for the image processing. In many applications, thermal cameras need to run on battery powered products, so it is important to perform image processing operations as efficiently as possible to reduce the power consumption. That makes PolarFire® SoC FPGA based ISP a powerful alternative for the other architecture-based ISPs available for thermal imaging systems.
In this case we used 640*480 VGA image sensor from Lynred as IR sensor and there is a proxy circuit which converts the analog signal to a digital bus. From there, we take it through a PolarFire SoC SoM developed by Digital core Technologies. The imaging pipeline (ISP) is implemented on the PolarFire SoC FPGA. The processor manages the Pipeline.
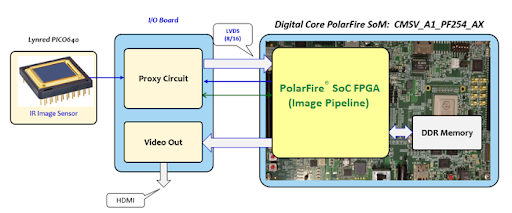
From the raw frames received from the sensor, we will not be able to distinguish anything. The thermal ISP pipeline takes this frame through a series of processes to generate a visual frame from which we can distinguish the thermal profile of the objects in the frame. The first level processes we do in the raw image are tone mapping, bad pixel correction, non-uniformity correction and image enhancement, such as digital filters. After that ISP normally apply image overlay and color palette to differentiate different temperature areas and regions. The output of the ISP is a human understandable thermal Image similar to that shown in the below image.
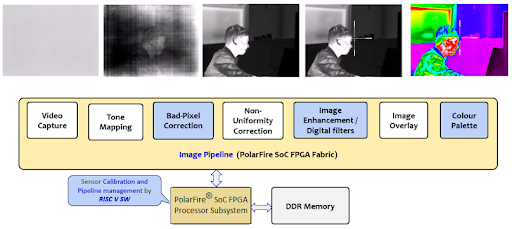
In summary, the advantages of developing thermal ISP core in the PolarFire FPGA SoC are:
- Low power consumption of the SoC
- Low power means less heat is generated in the product, which is crucial for the performance and stability of thermal cameras
- Flexibility in tuning and customizing the ISP as it is implemented in FPGA
- Ample CPU resources for embedded camera application
- Compact design and low cost
Please visit Digital Core Technologies website www.dicortech.com or core modules website page for more info regarding thermal ISP development or email us at info@dicortech.com for detailed information about the PolarFire/ RISC-V based developments like the thermal ISP. For more information on our PolarFire® SoC FPGAs visit our website.